Industry Leading Commercial
Freeze Dryers
At Parker Freeze Dry, our line of commercial freeze dryers can fit any need. Whether you’re scaling up from a countertop unit or looking to exponentially increase your pounds of product per batch, we can help you grow. From our Summit line with a maximum capacity of 97 lbs. per batch, to our industrial sized Parker units with up to 4000 lbs. per batch, you are sure to find the solution to take your operation to the next level.
Our commercial freeze dryers are perfect for processing batches for many industries including, but not limited to: pharmaceuticals, pet food, CBD/hemp/cannabis, cosmetics, food processing and more. With our innovative equipment design and dedicated service, you can rely on Parker Freeze Dry to help take your freeze drying operation to the next level.
Commercial Freeze Dryers
More Product. More Profit.
Enter some business metrics to find out the Parker Freeze Dry unit that suits your needs, and your estimated gross margin per pound.
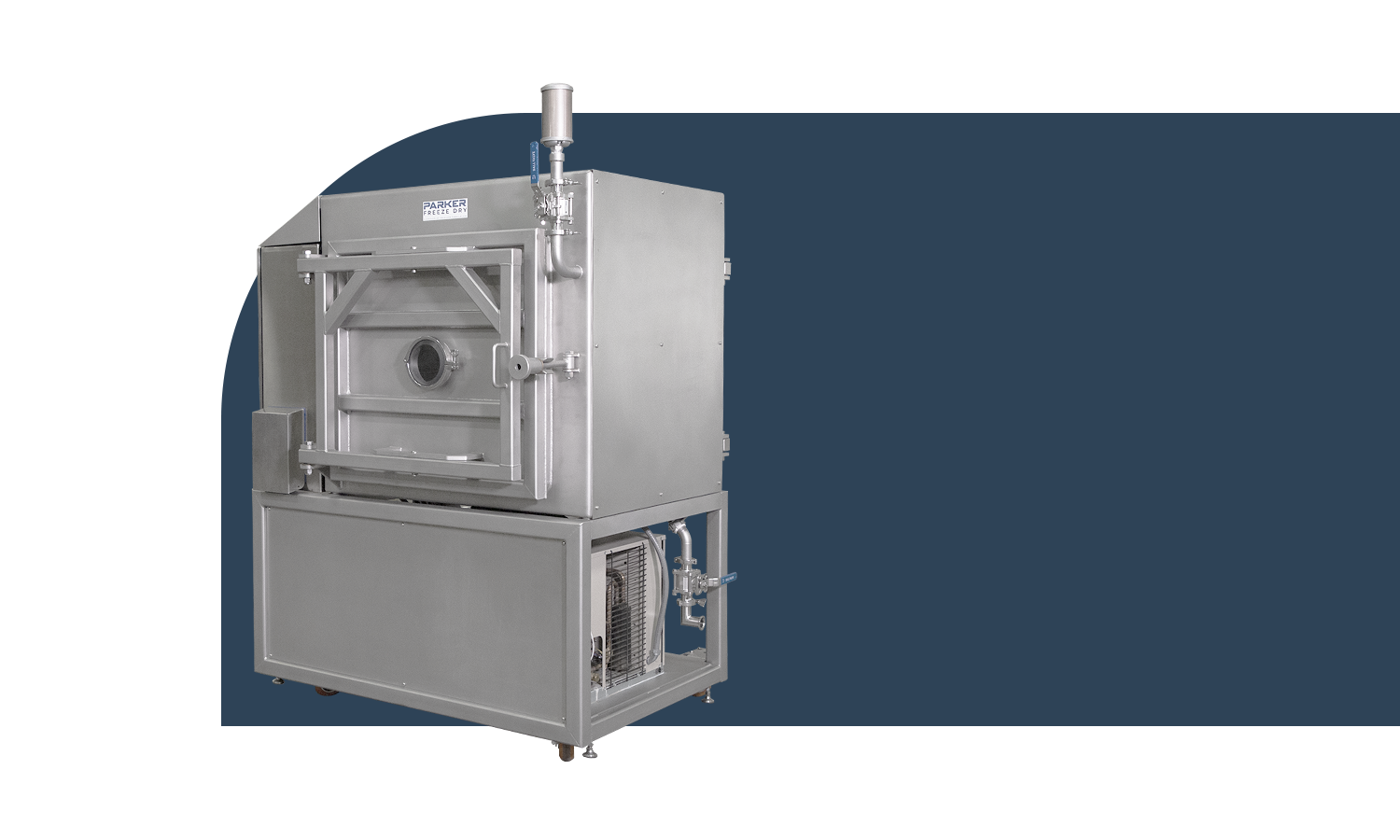
Summit Freeze Dryer
The Summit freeze dryer is perfect for operators looking for commercial quality freeze drying equipment in a turnkey package. With a wet volume of 97 lbs utilizing a maximum of 15 individually heated trays, Summit users will experience consistent results.
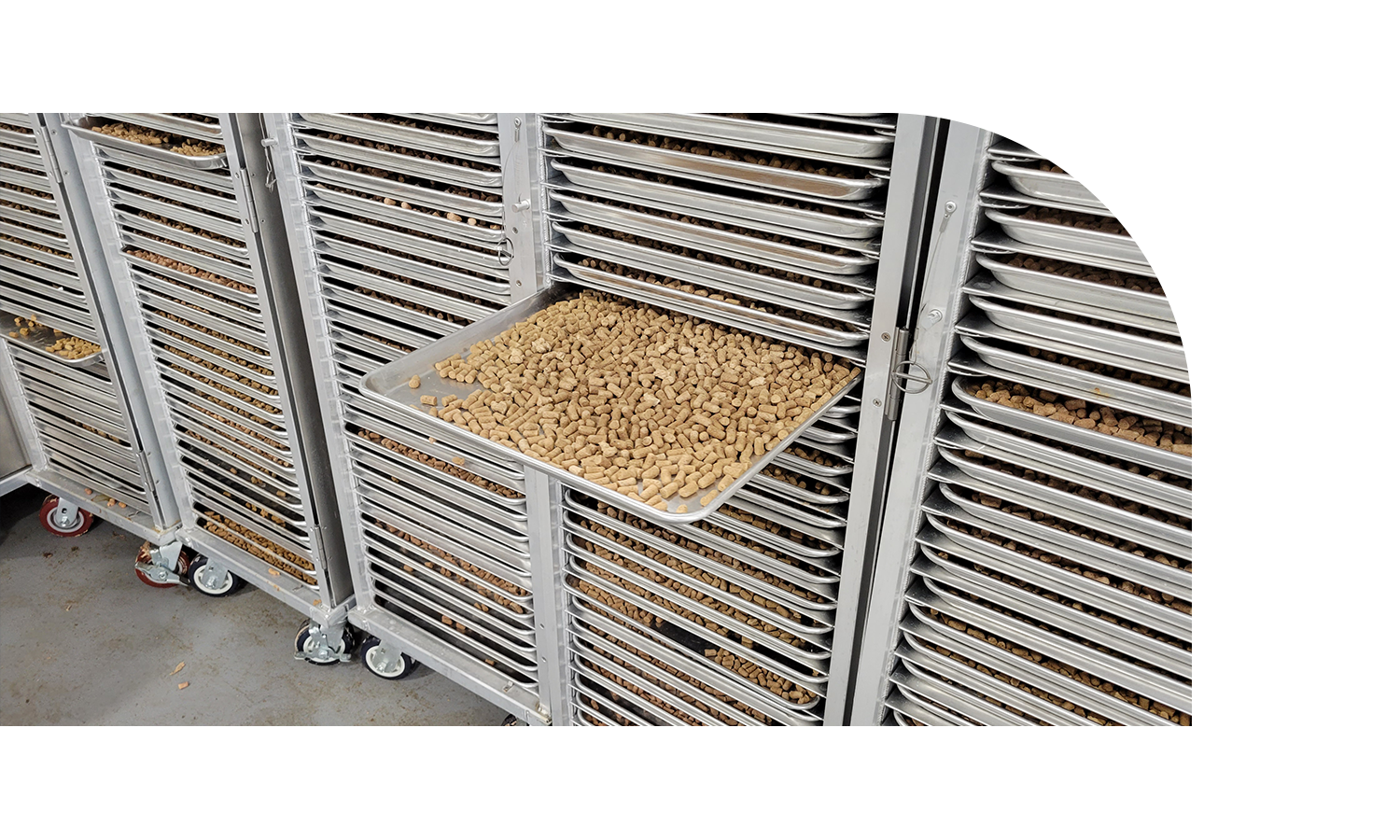
Why Freeze Dry?
Freeze Drying Options for Every Industry
Unleash the potential of freeze drying in various industries, from agriculture and bioengineering to nutraceuticals and pet food. Explore the applications for a commercial freeze dryer.
Let's Get Started
Our commercial freeze dryers range in batch sizes from 97 lbs to 4000 lbs, all with advanced vacuum systems, industry-leading controls and vapor condenser plates. Take your commercial operation to the next level by finding the perfect sized custom built unit for your specific needs.